Metal Fabrication Melbourne: Precision Design for All Demands
Metal Fabrication Melbourne: Precision Design for All Demands
Blog Article
Ingenious Patterns in Steel Fabrication: Enhancing Toughness and Precision
In the realm of steel fabrication, the pursuit of longevity and accuracy has brought about a wave of ingenious trends that are improving the industry. From advancements in welding modern technologies to the combination of robot automation in construction processes, the landscape of steel manufacturing is developing swiftly. High-strength alloy advancement, coupled with the use of 3D modeling and simulation software application, is pressing the boundaries of what is possible in regards to structural integrity and precision. Moreover, the expanding emphasis on lasting techniques in steel manufacturing is not just driving performance but also fostering a much more eco mindful strategy to fabrication. These patterns are not simply forming today however likewise laying the foundation for the future of steel fabrication, guaranteeing more enhancements in resilience and precision.
Advanced Welding Technologies
In the realm of steel construction, the adoption of sophisticated welding modern technologies has dramatically reinvented the industry's technique to attaining superior high quality and accuracy in structural welds. Advanced welding innovations, such as laser beam welding and friction mix welding, have actually become game-changers in the field. Laser light beam welding employs a focused laser beam of light to join steel parts with impressive accuracy and rate, making it ideal for thin materials and detailed layouts. On the other hand, friction mix welding produces extremely strong bonds by mechanically intermixing the particles of the products at the joint, getting rid of the need for thawing the steel. These modern technologies use many benefits, consisting of minimized heat-affected zones, marginal distortion, and boosted mechanical properties in the bonded joints. By leveraging these sophisticated welding techniques, steel makers can raise the resilience, toughness, and accuracy of their structural welds, satisfying the increasingly requiring demands of modern building projects.
Robotic Automation in Manufacture
Embracing robot automation has actually become a foundation of modern-day steel fabrication practices, enhancing processes and boosting efficiency throughout the industry. Robots are revolutionizing the method steel elements are made, offering exceptional accuracy and rate while lowering human error. These automated systems can handle repeated tasks with constant accuracy, causing better output.
One key advantage of robotic automation in steel fabrication is the ability to work around the clock without fatigue, considerably enhancing production outcome. This constant operation reduces downtime and speeds up job timelines, eventually saving costs for manufacturers. Additionally, robots can be set to execute detailed jobs that might be dangerous or difficult for human workers, boosting safety and security in the office.
Additionally, robot automation enables smooth assimilation with other electronic modern technologies, such as computer-aided design (CAD) software application and Net of Things (IoT) systems (steel fixing). This interconnected approach improves interaction in between various stages of fabrication, enhancing operations and ensuring real-time monitoring and control. As the steel construction market remains to evolve, robotic automation stands apart as a transformative i was reading this force driving effectiveness and accuracy in making procedures
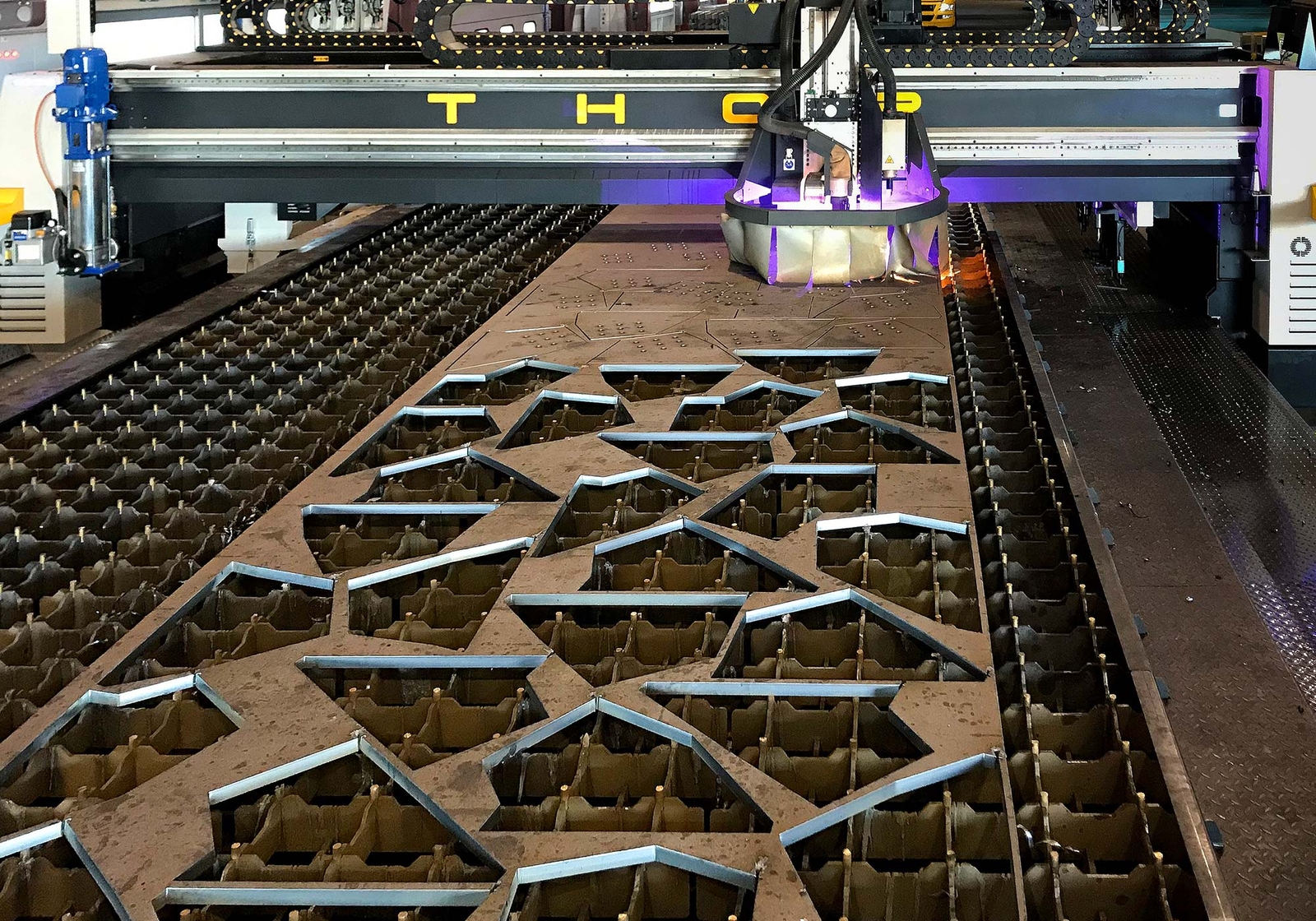
High-Strength Alloy Development
The advancement of high-strength alloy advancement in steel fabrication is improving this article the sector's approach to improving product durability and performance. High-strength alloys are engineered to show superior mechanical residential or commercial properties, such as enhanced tensile strength, toughness, and corrosion resistance compared to typical steel qualities. By integrating these sophisticated alloys into fabrication processes, suppliers can generate elements that endure higher stress degrees and rough atmospheres, resulting in more trusted and sturdy final product.
One key advantage of high-strength alloy advancement is the ability to lower product thickness without endangering structural integrity. This not just leads to lighter-weight parts however also adds to cost financial savings and enhanced efficiency in manufacture and assembly procedures. The improved strength-to-weight proportion of these alloys enables for the layout and construction of frameworks with higher load-bearing capabilities while minimizing general weight.
3D Modeling and Simulation Software Program
Innovations in steel fabrication processes have been significantly pushed by the combination of innovative 3D modeling and simulation software program devices. These devices enable producers to produce comprehensive online designs of their projects, enabling them to visualize the final item with accuracy prior to any type of physical work begins.
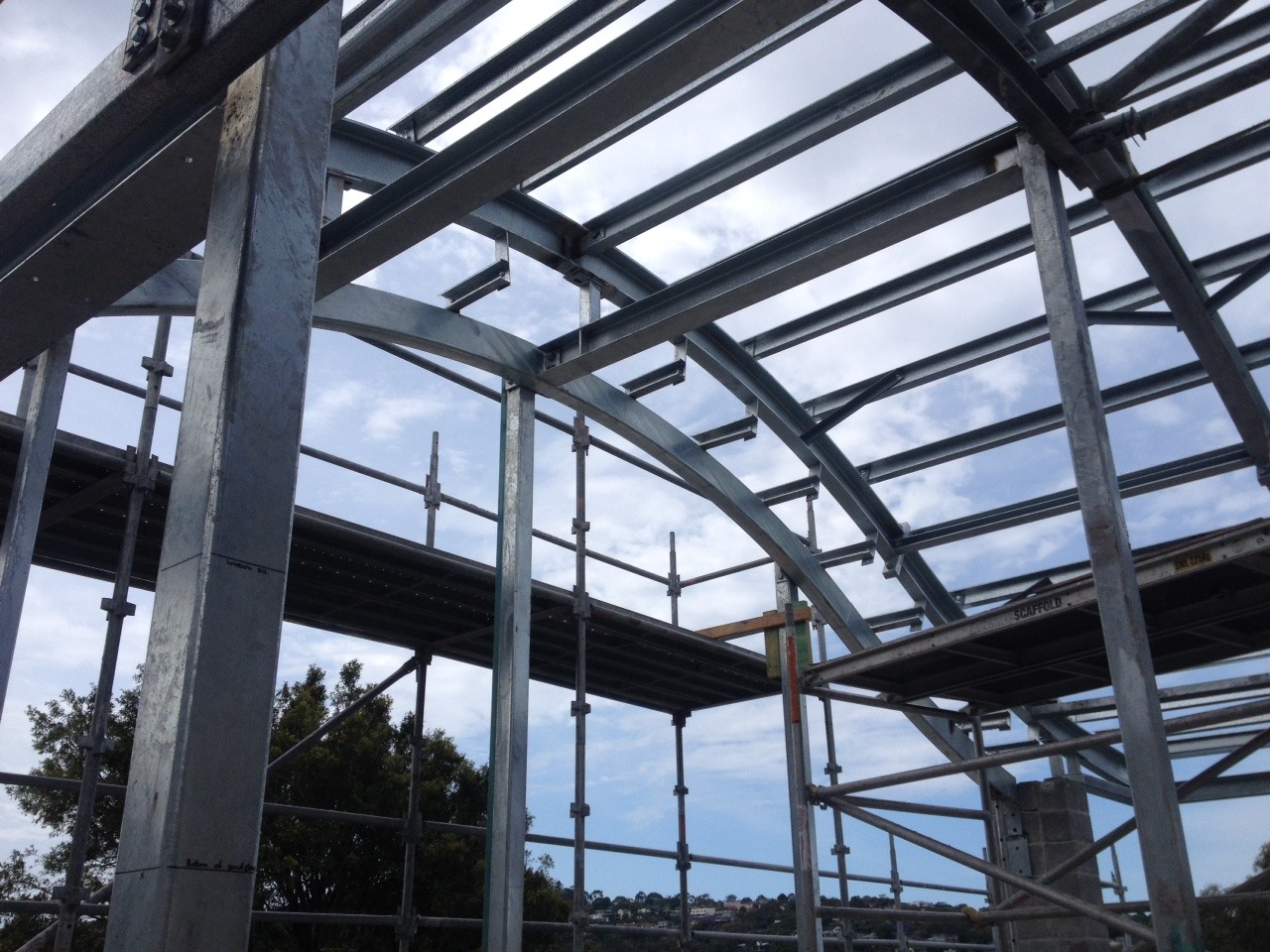
Sustainable Practices in Steel Production
Including lasting methods right into steel production procedures is necessary for reducing environmental effect and ensuring long-lasting source accessibility. One vital sustainable method is the fostering of energy-efficient innovations to lower greenhouse gas emissions during the steel production process. This includes utilizing renewable energy resources, such as solar or wind power, to power steel plants and implementing energy-efficient devices to optimize energy use.
Another important facet of sustainable steel production is the accountable sourcing of resources. This entails guaranteeing that the iron ore and other sources made use of in steelmaking are obtained from ethical and ecologically pleasant sources. By promoting transparency in the supply chain and adhering to stringent ecological criteria, steel manufacturers can reduce the unfavorable effects of source removal on neighborhood ecosystems and communities.

Final Thought
In conclusion, the innovative fads in steel construction such as sophisticated welding technologies, robotic automation, high-strength alloy growth, 3D modeling and simulation software application, and sustainable methods are improving the toughness and accuracy of steel products. These developments are revolutionizing the steel fabrication sector by enhancing top quality, effectiveness, and sustainability. It is clear that the future of steel fabrication depends on embracing these sophisticated innovations to fulfill the demands of modern-day building and production markets.
In the realm of steel manufacture, the pursuit of durability and precision has actually led to a wave of innovative fads that are reshaping the sector.In the realm of steel manufacture, the adoption of innovative welding modern technologies has dramatically transformed the sector's approach to attaining superior high quality and accuracy in structural welds. As the steel construction sector continues to progress, robot automation stands out as a transformative force driving effectiveness and precision in producing procedures.
Additionally, recycling and recycling steel scrap and waste products play a considerable role in enhancing the sustainability of steel production. steel fabricators melbourne.In verdict, the innovative trends in steel construction such as sophisticated welding modern technologies, robot automation, high-strength alloy development, 3D modeling and simulation software application, and lasting techniques are boosting the sturdiness and accuracy of steel items
Report this page